Over the last month, work has continued on the Worthington pump replication project with the focus having briefly turned to the reproduction of many of the bronze components from the pump, which includes the steam exhaust flange, tappets, lock nut, spindle valves, and several other pieces. Similar to the mold making method used to copy the steam chest cover and dampening piston cylinder head cast last April (see April blog posts), rubber molds were taken of the components through a several stage process. However, instead of using the technique of piece mold pattern casting, the “lost wax” casting method was employed to replicate the parts along with a different type of furnace used to melt the metal.
I’ll use the steam exhaust flange to describe the overall process.
The object was first sealed in several layers of a fine wax to act as a barrier between the artifact and molding materials. Then, dental wax was placed in the holes within the object to separate it into two halves.
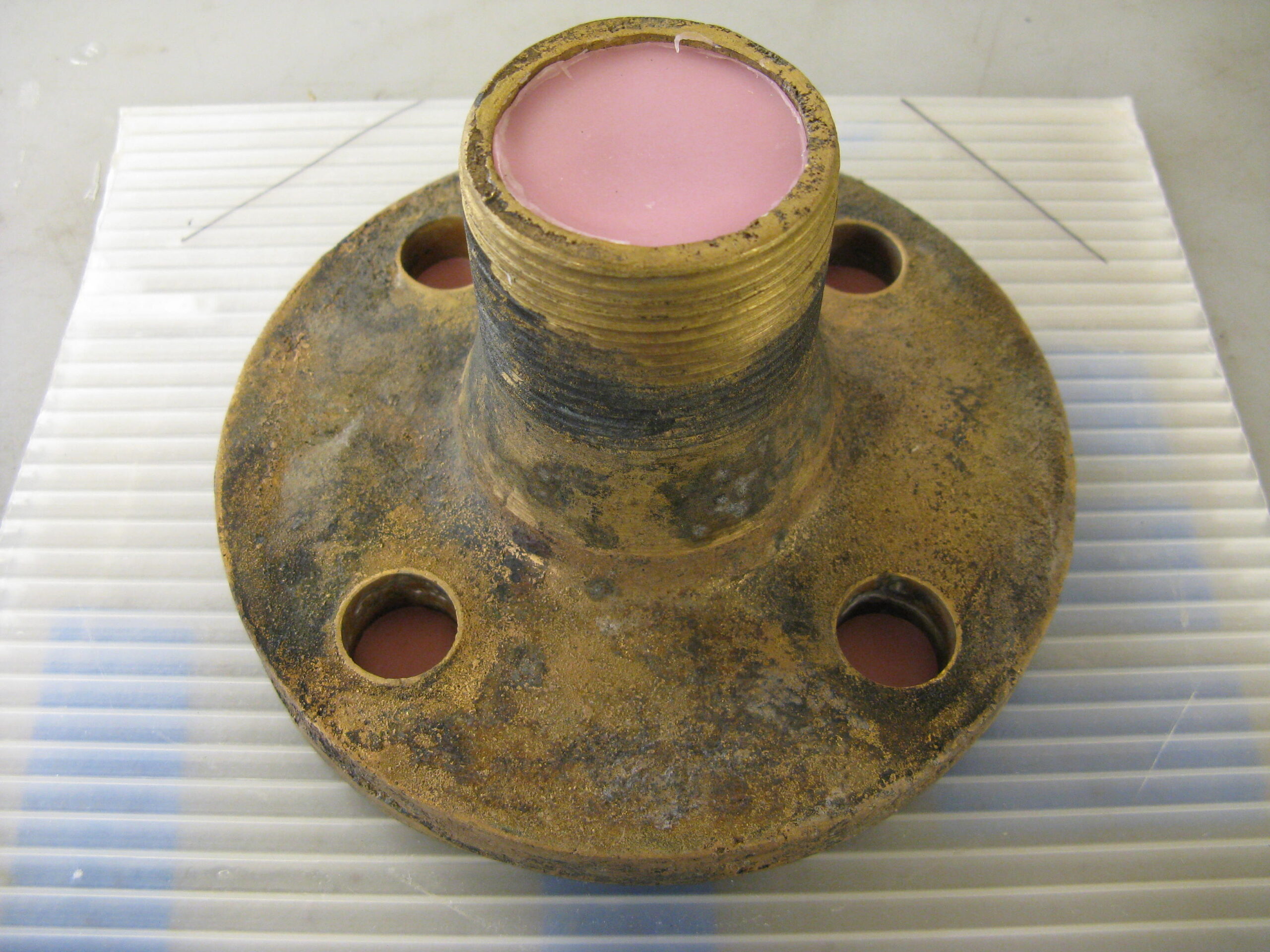
The component was then covered with a liquid rubber, which copied the surface detail of the artifact.
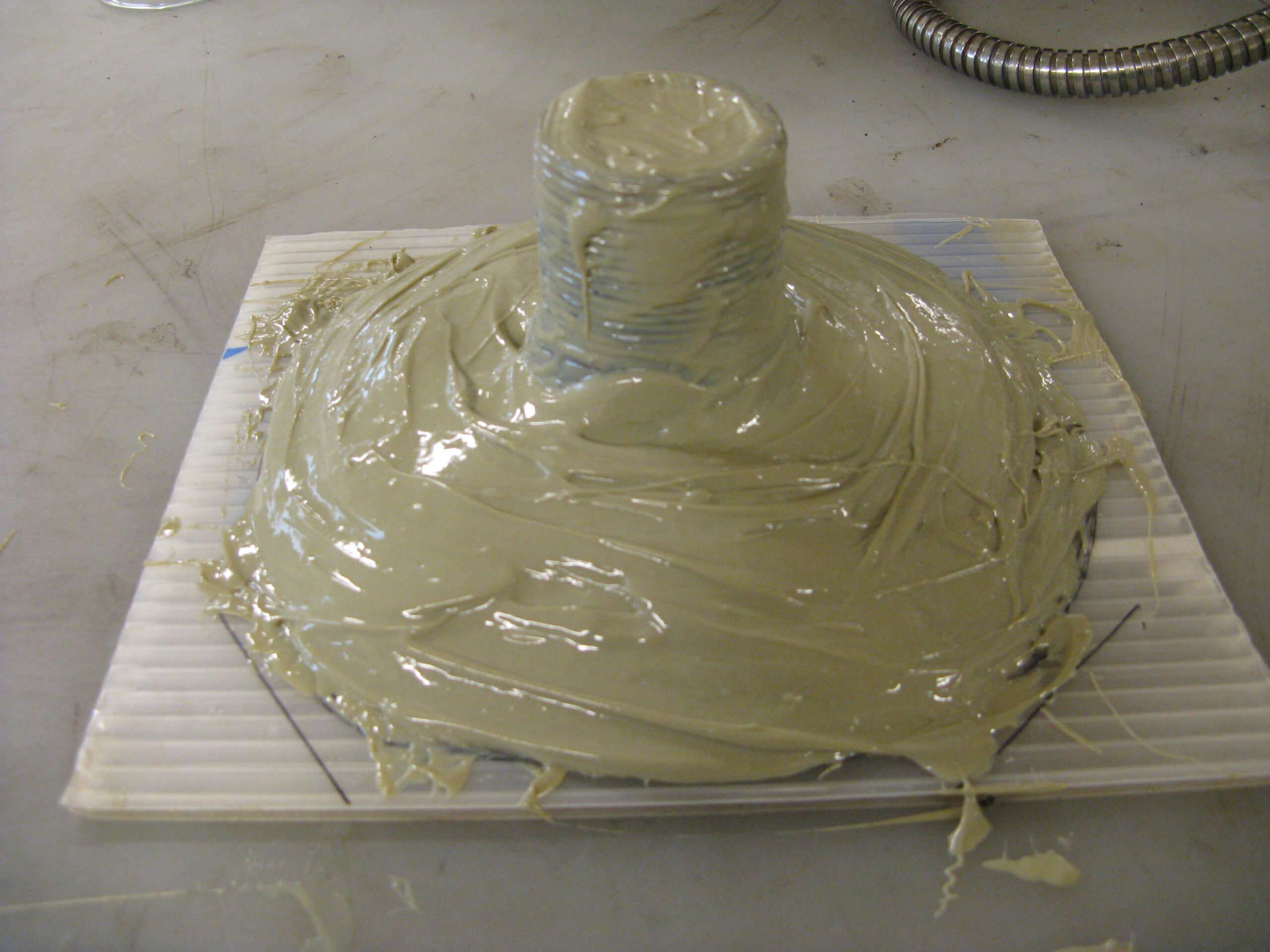
After several application of rubber, a box was placed around the artifact and the area within it was divided into two parts.
Plaster was then poured into one of the two cavities.
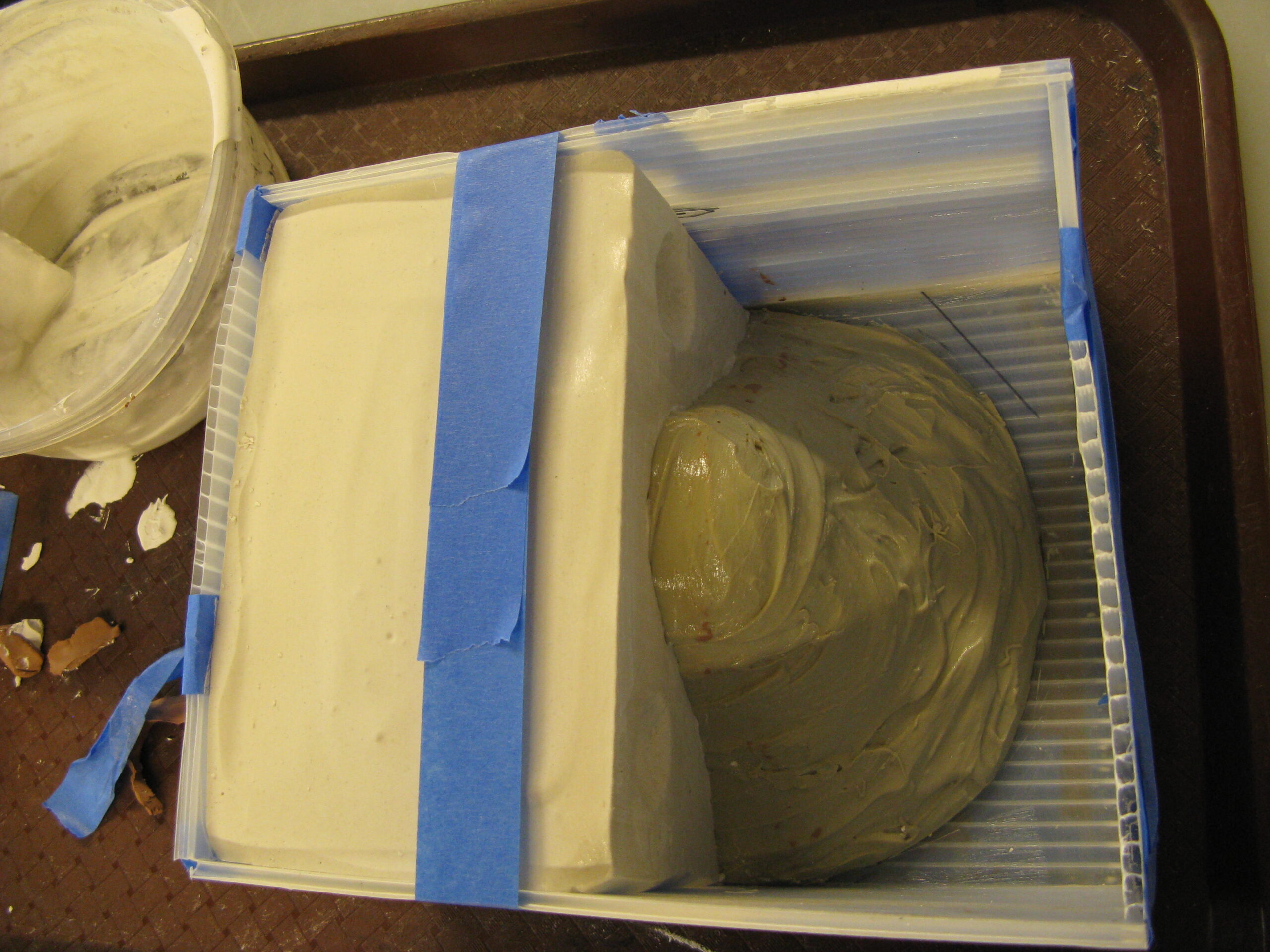
After the plaster had set, the barrier was removed and plaster was poured on the other side of the interior cavity. The reason for using the plaster, which is referred to as a “jacket” is to hold the rubber mold material in place once the artifact is removed from it. With both plaster sides poured and set, the mold was turned over to expose the bottom surface.
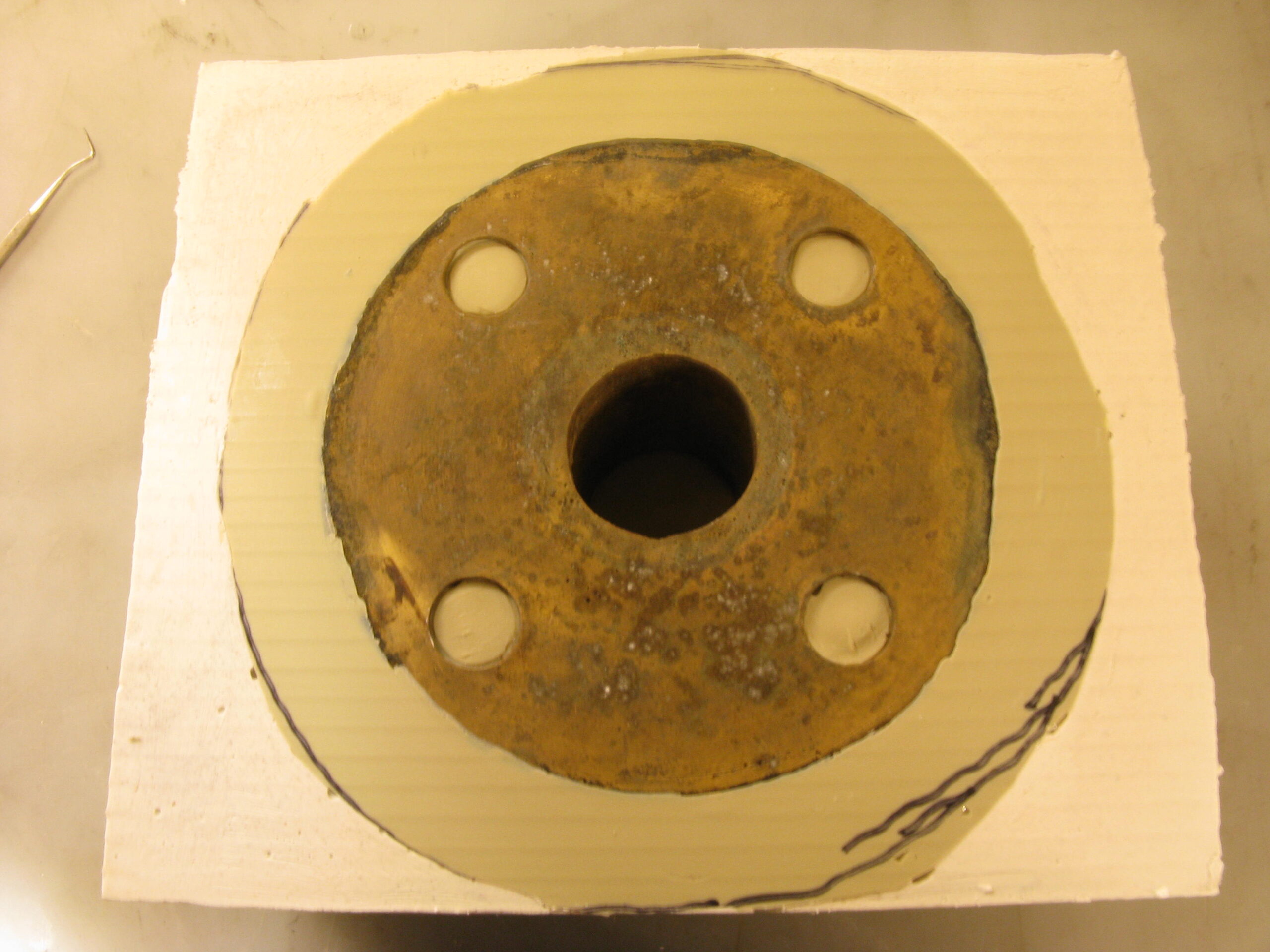
With the bottom surface in view, the dental wax was removed and it was covered with liquid rubber, followed by plaster.
After the final layer of plaster had set, the mold was taken apart and the artifact was safely removed creating a negative copy of the object in rubber.
Next, the mold pieces were reassembled and held in place by large clamps.
Then, wax designed for metal casting was poured through a whole in the side of the mold to make a detailed wax copy.
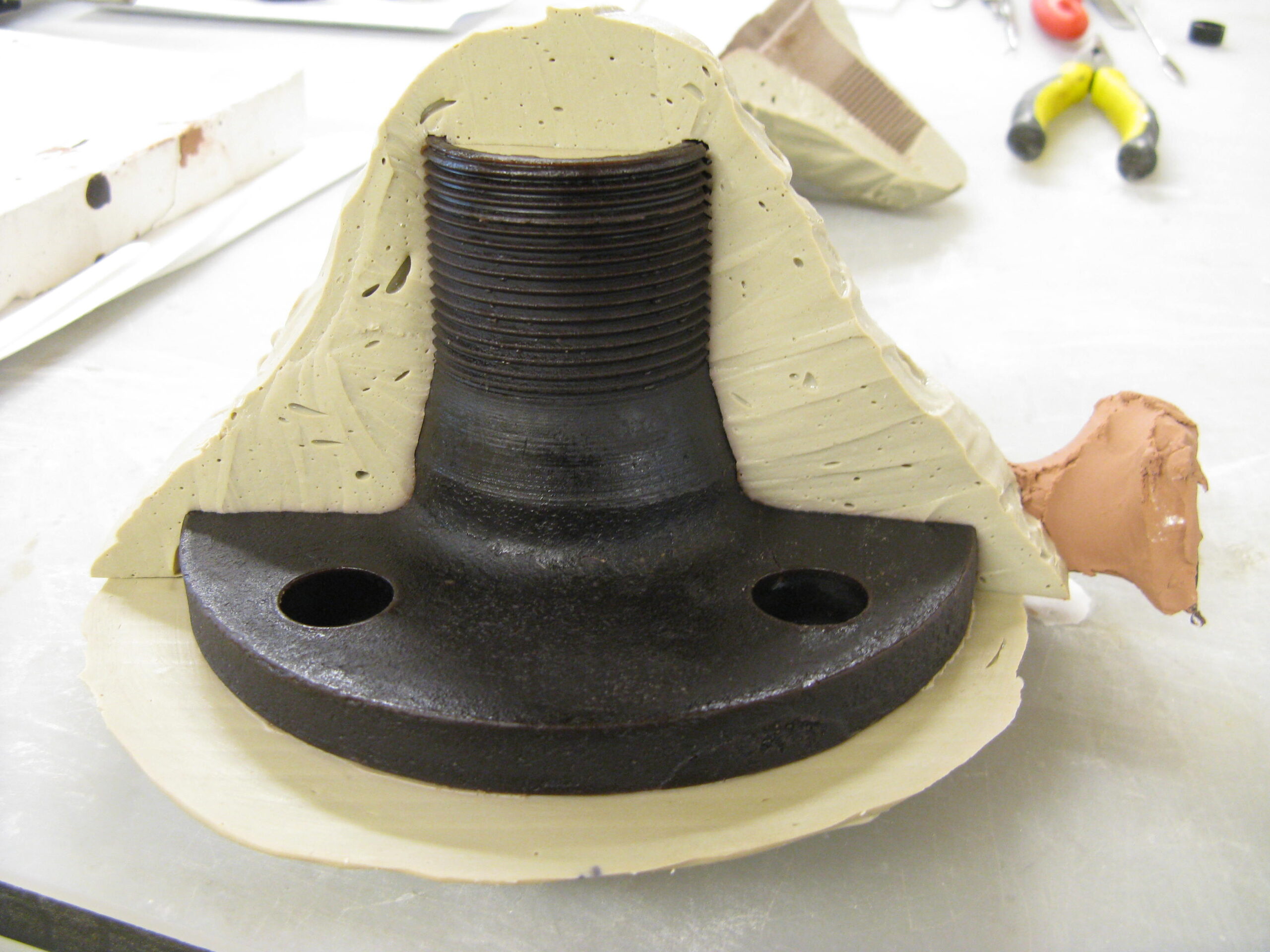
A view of the the wax copy in the above image with a portion of the mold removed.
This same method was repeated for the rest of the objects.
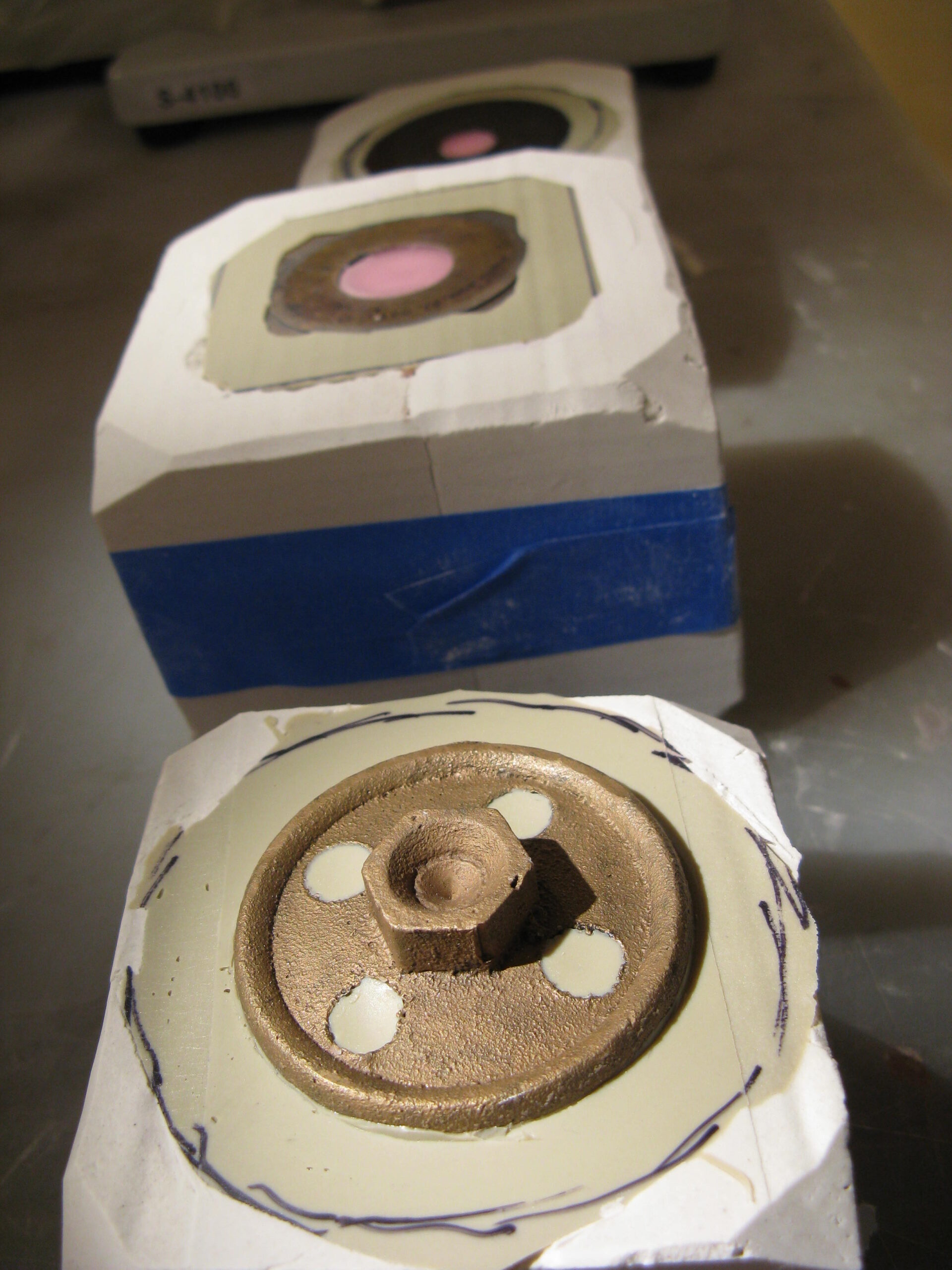
The image above shows half-completed molds with the spindle valve in focus.
Waxes were then made for all objects.
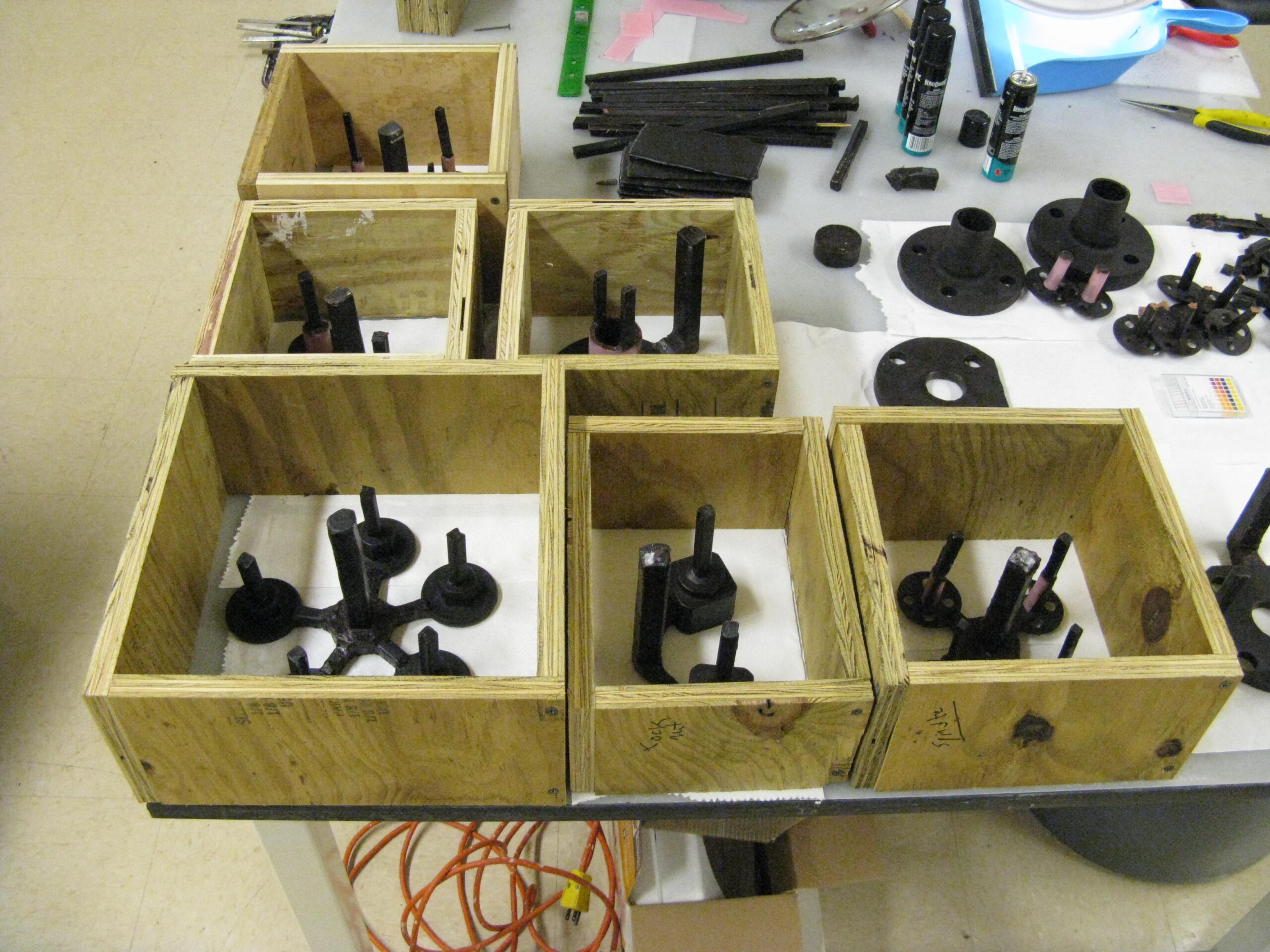
This image shows the completed waxes with their “pour systems” attached and set in flasks ready to be pack with sand at the foundry.
Many more images to be posted soon!!!!!!