Continuing from the post made on November 30th……I know you have all been waiting!
Once the wax copies had been completed at the Mariners’ Museum, they were packed up and transported to the foundry at Buffalo state College.
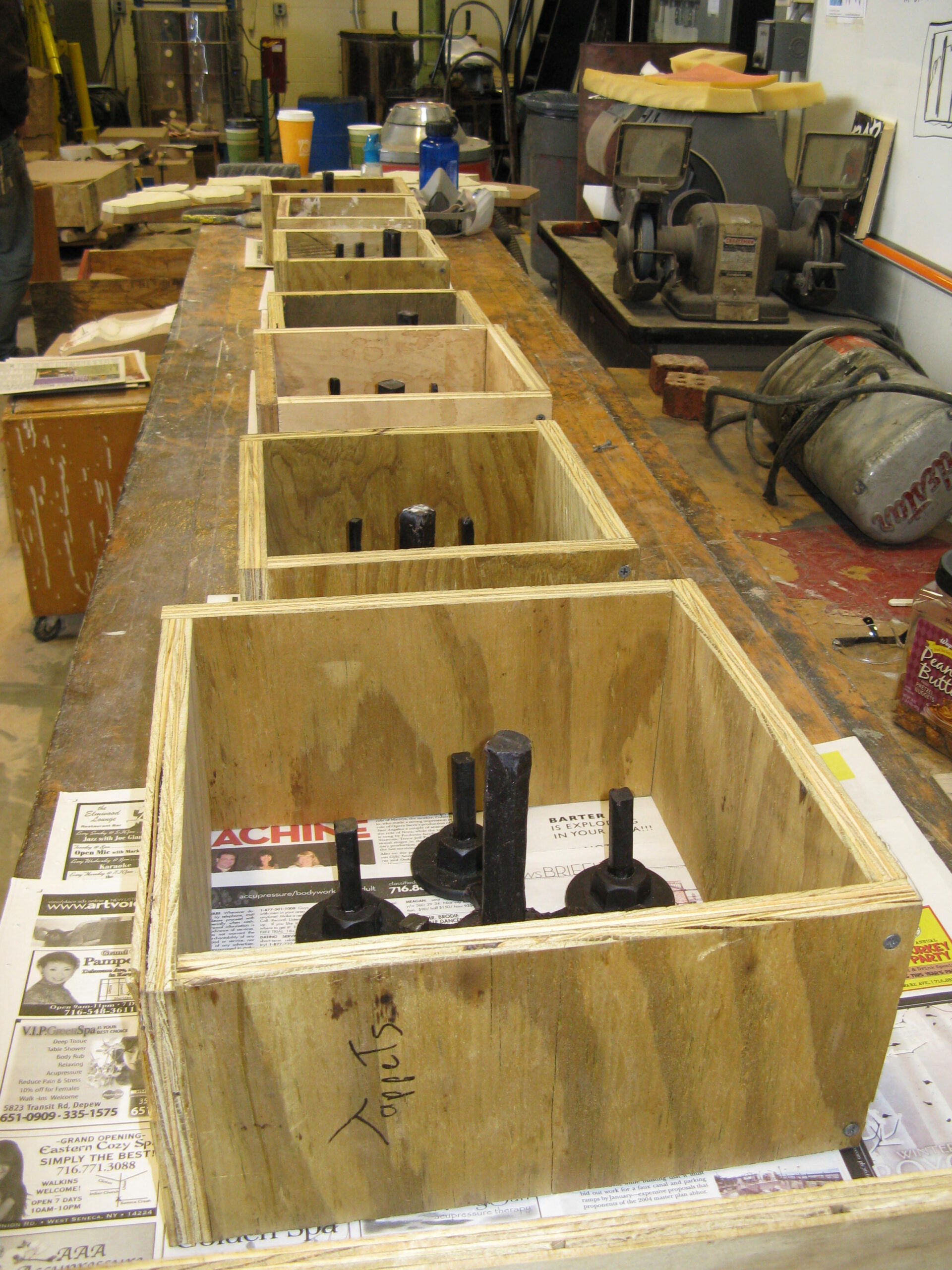
Upon arrival, the casting flasks (wooden boxes) were setup around each of the waxes and fine sand mixed with resin and a catalyst was carefully packed around the objects.
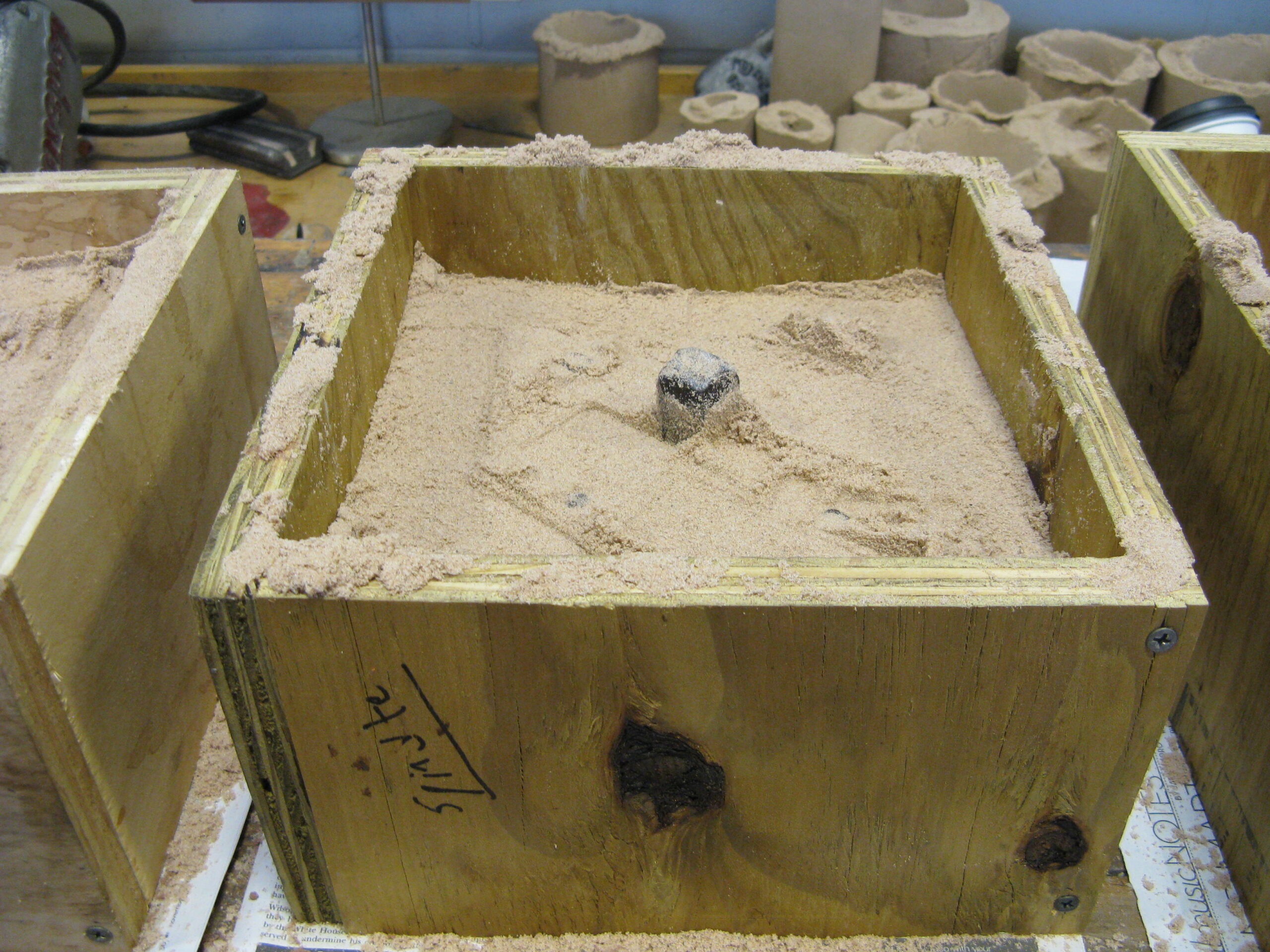
After the sand had cured, the molds were turned over and the opposite sides were packed with sand.
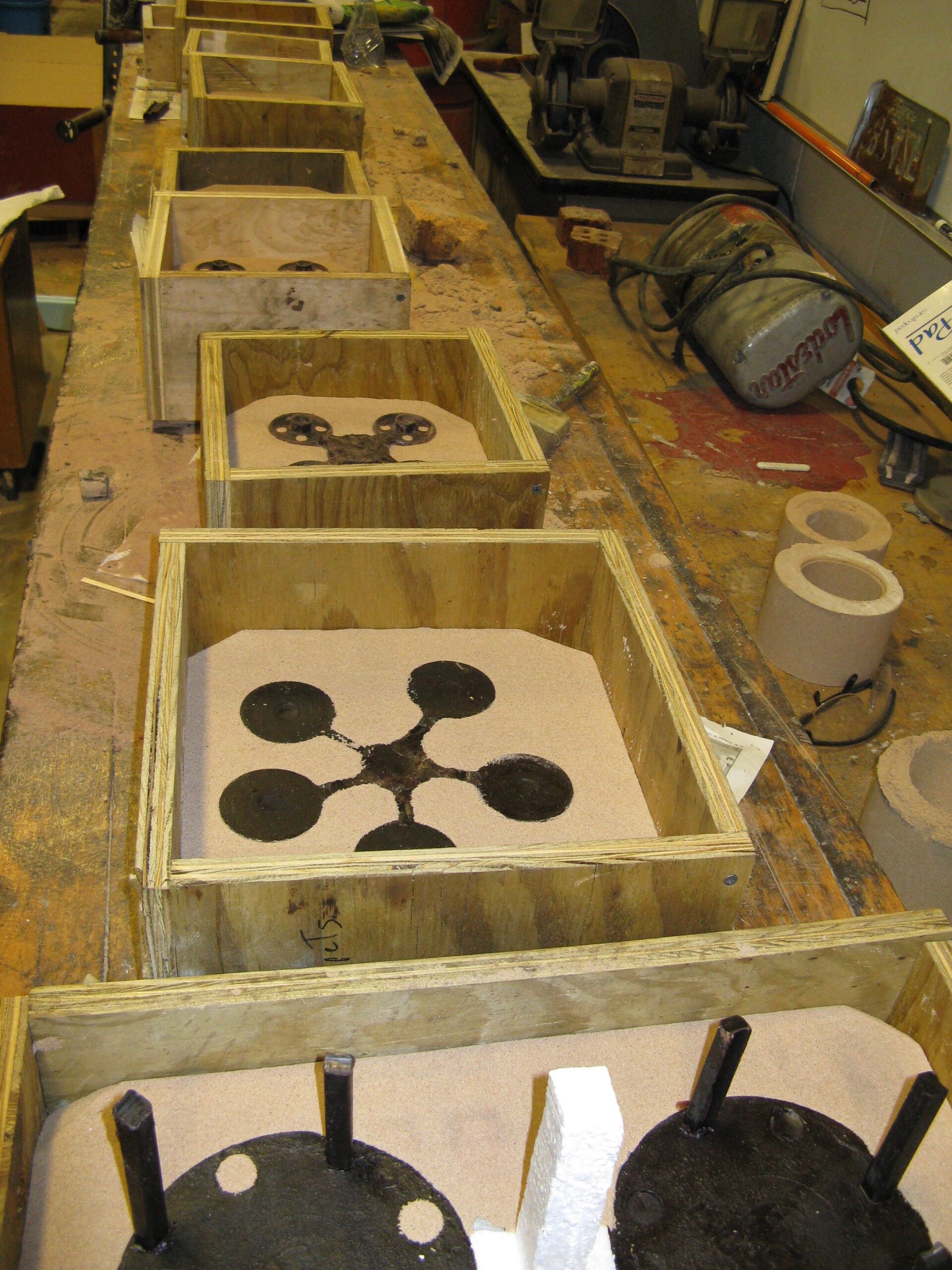
Once the molds were complete, metal banding was placed around each one to ensure that they would not come apart during the rest of the casting process.
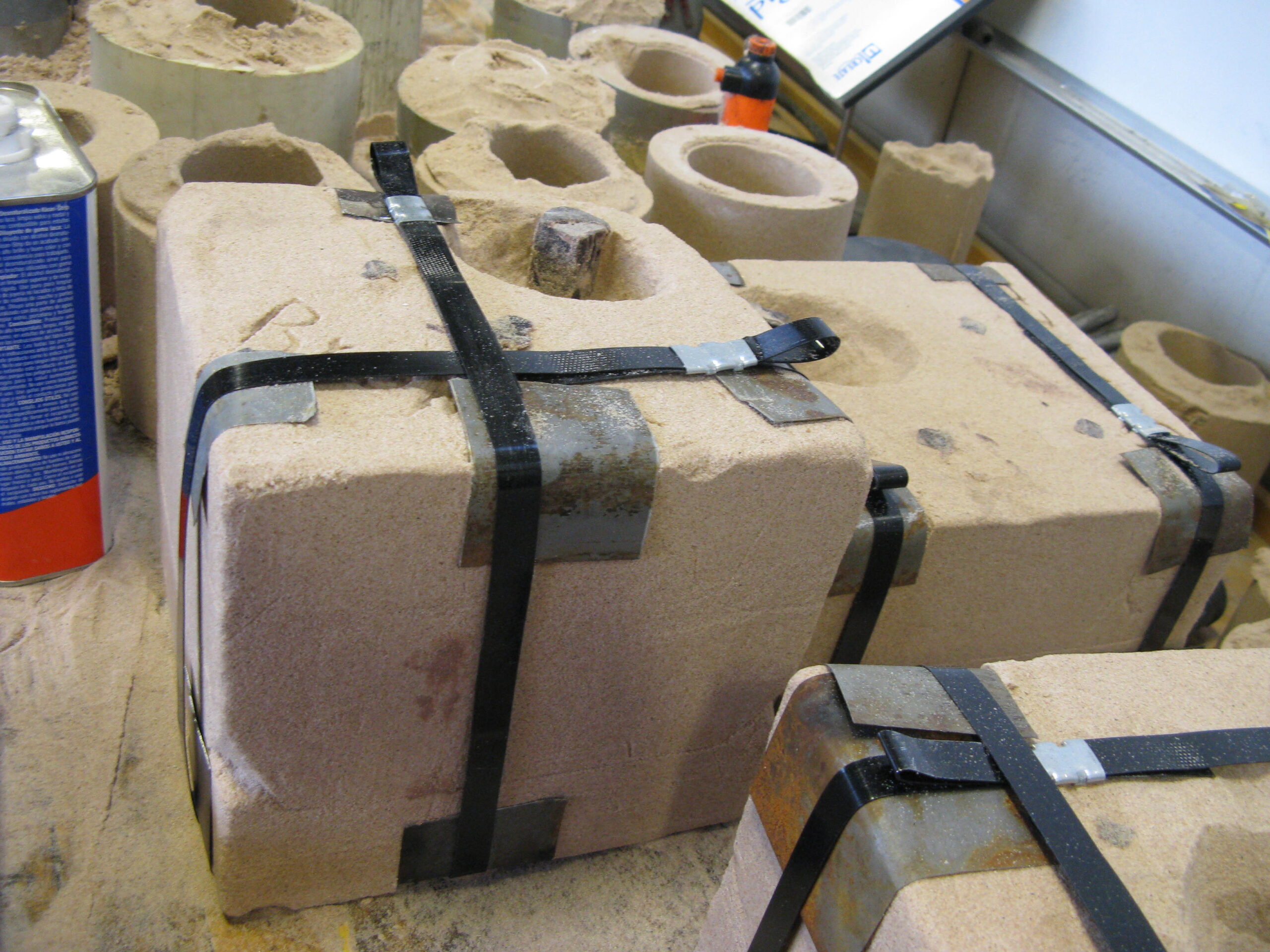
The completed molds were placed into a brick-lined kiln for ten hours at 300 degrees Fahrenheit. At that temperature, the wax was vaporized leaving behind negative copies of the object within the sand (one can see the now hollow pour systems in the lower image). This technique is referred to as the “lost wax” method of casting.
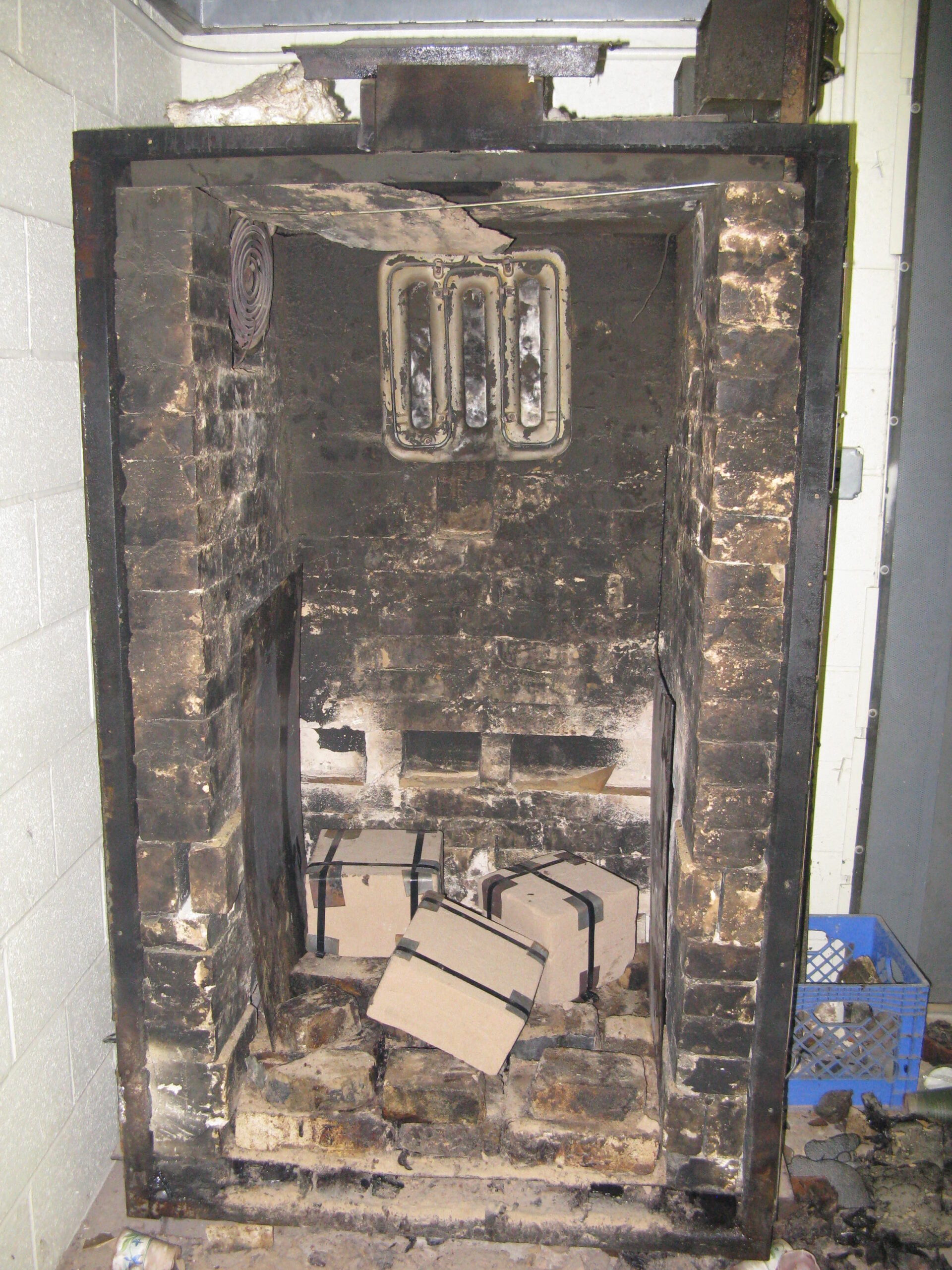

The competed molds were now ready to be filled with bronze.
To carry out the next phase of the project, much thanks must be given to John Cerra, who is the owner of IGT Custom Gears (http://www.igtcustomgearcutting.com/index.html) who donated approximately 70 pounds of old bronze gears and rod (see below). John is also graciously helping with other aspects of the project including CAD work and thread cutting (blog posts to follow).

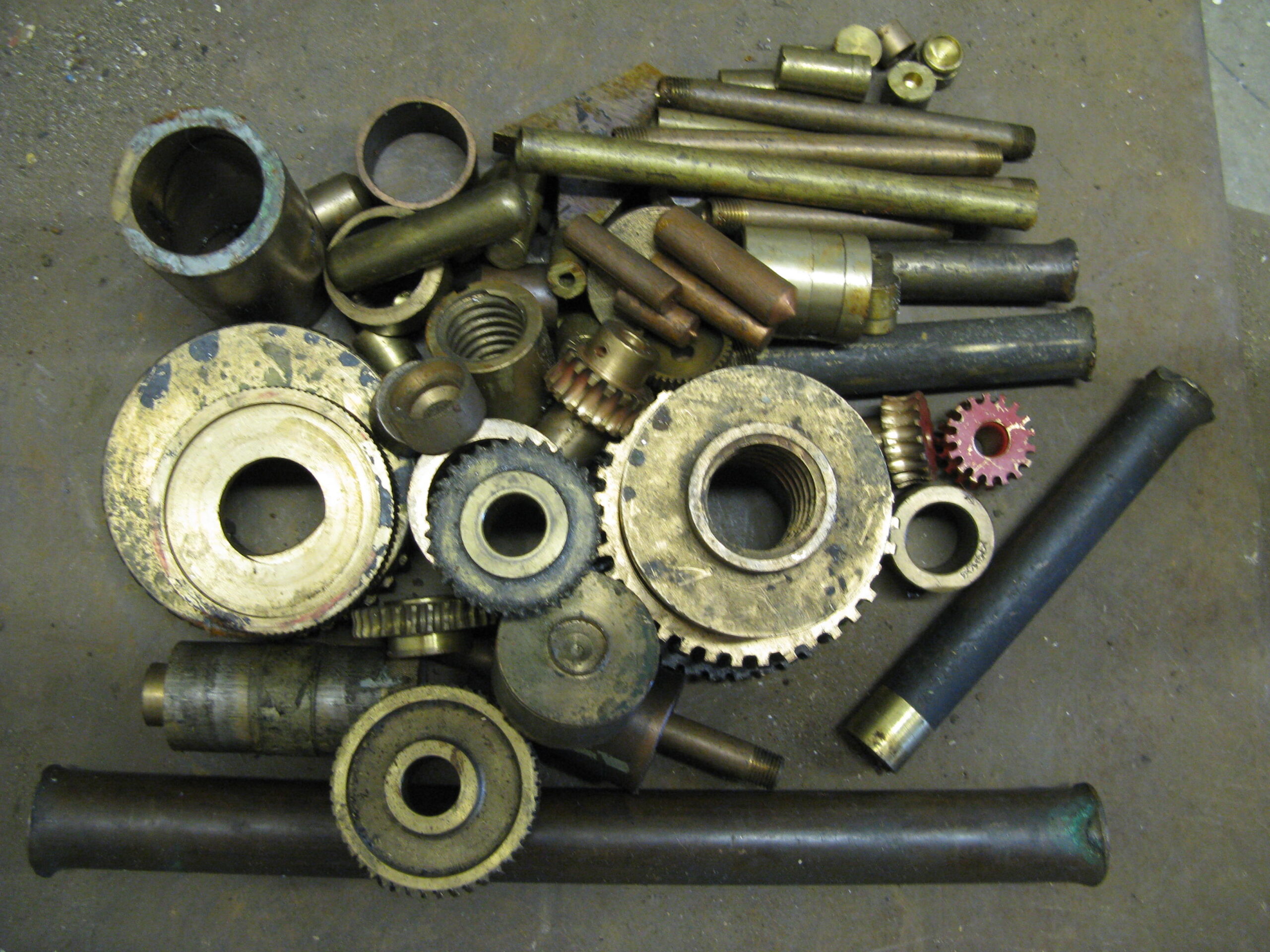
That is it for now, check back later this week for the third installment of Going for the Bronze!!!!