Although my blogs to date give a very Dahlgren-centric view of what I do, there is far more to USS Monitor than just its guns. And I love having such a huge variety of objects to work on! In addition to big metal objects, we find a wide variety of organic objects, ranging from the wooden sides of the gun carriages to rope packing seals to a wool coat. We also have a number of brushes from on board the ship, including a nearly complete bench brush that I’ve been working on!
This brush was originally found stuck to one of the gun carriages, covered in mud and concretion – the hard, rocky material that forms around corroding iron. Although the brush itself is entirely organic – wood and fiber – it was so close to the iron of the gun carriage that it was caught inside concretion formed by that object. As a result, it didn’t look like much to begin with.
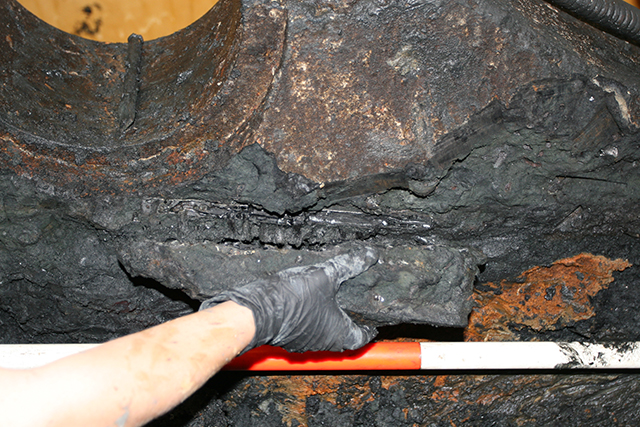
At first glance, this looked like a brush with some bristles still in place, but it didn’t look complete. However, when working on concreted objects it is often difficult to tell exactly what you have just by eye; the first step in working on an object like this is x-radiography, which helps us to know what’s actually there. With this brush, radiography revealed that nearly the entire object – including all of its bristles – was likely still present!
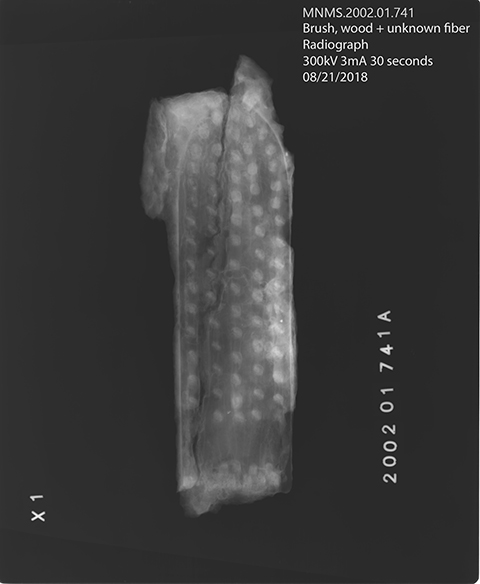
And with the imaging in hand, it’s time for a visit to the dentist!
…wait… what?!
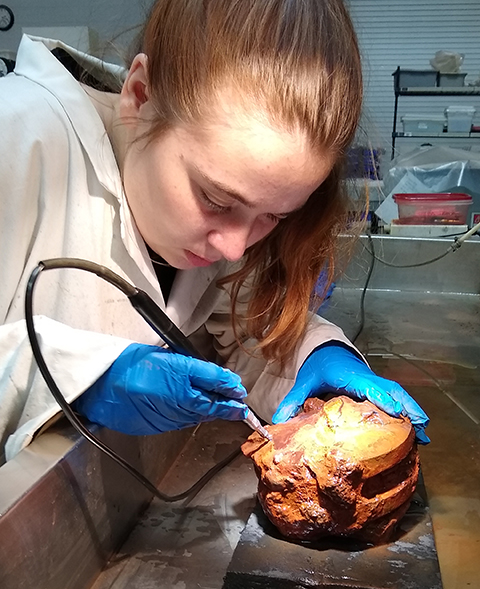
A huge number of the tools we use are co-opted from other professions, and with organics, we take a lot from dentistry. The bulk of concretion on this brush was removed using an ultrasonic dental scaler, and softer material was removed using a water flosser and dental picks. Some extremely hard material was also removed using a small pneumatic chisel called an air scribe… that one’s not a dental tool, and you should probably avoid anyone who suggests otherwise. Just trust me on that one.
The wooden sections were cleaned first since they are stronger than the brush bristles. Cleaning the back side of the brush first would make it easier to sit flat while cleaning the more delicate bristles on the front.
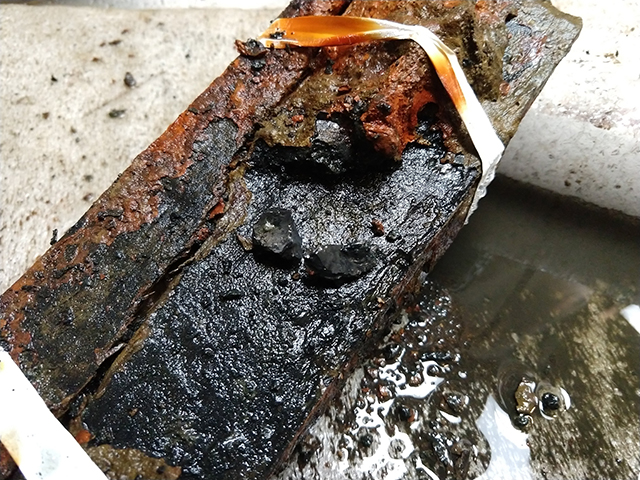
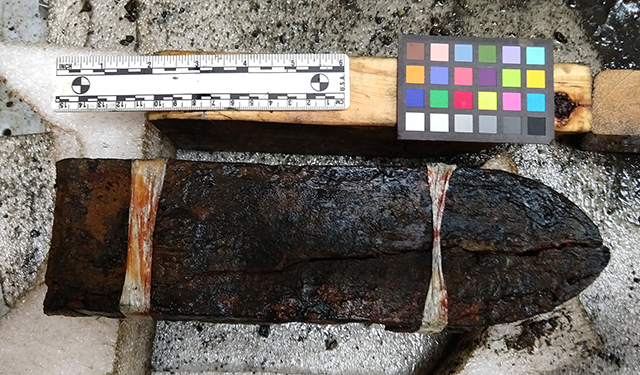
The bristles were a little more complicated than their wooden backing. The fibers making up each bristle are extremely fragile, and are held together in large part by the mud and concretion around them. As a result, removing the concretion without destroying the bristles was a slow, difficult process. By alternating mechanical cleaning methods like the dental scaler with chemical methods to soften concretion, it was possible to slowly uncover the front side. Supports had to be constructed at several stages for the brush itself and for individual clusters of bristles, just to make sure everything stayed in place while the brush was being cleaned.
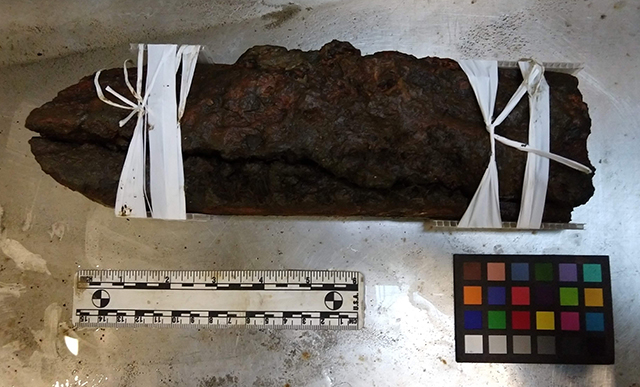
Although the two pieces of brush were kept together while cleaning the back side, it was easier to clean the front with them separated. In order to work on the pieces separately, they required supports along the broken edges, which were made from a waterproofed plaster bandage.
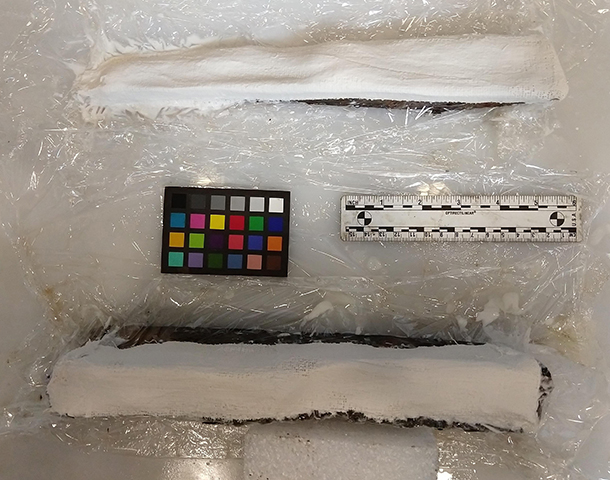
With some supports in place, it was possible to start cleaning:
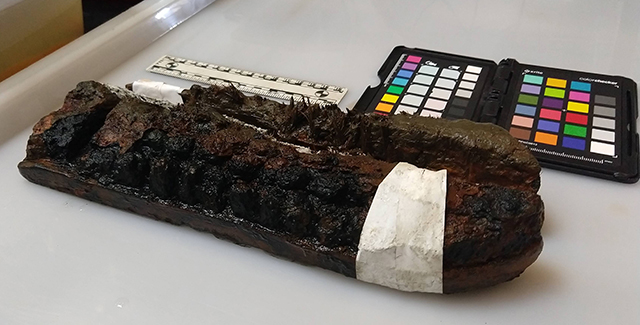
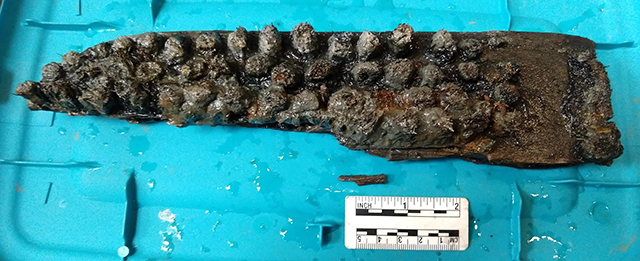
In addition to supporting the damaged areas of the brush’s structure, it was necessary to support some of the individual bristles as cleaning progressed – otherwise they want to float away in wet storage!
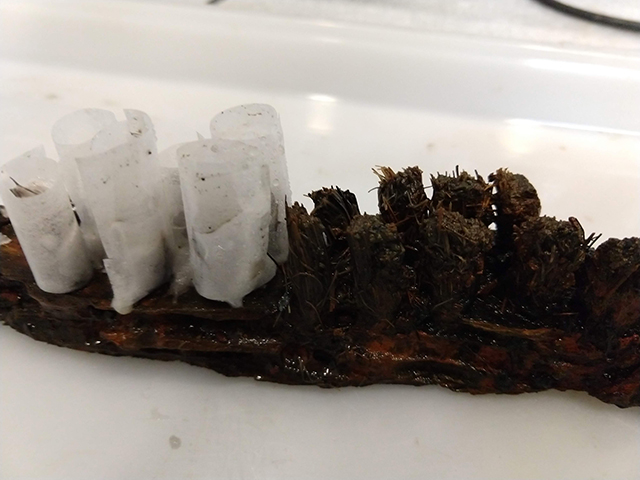
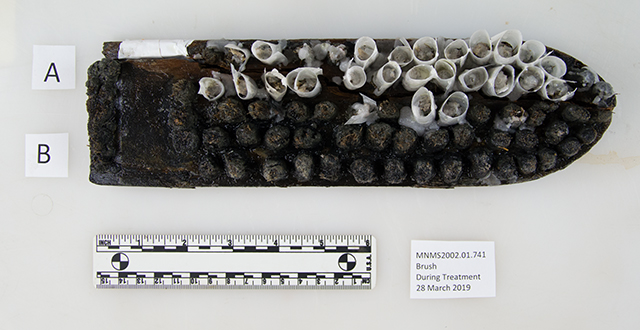
The exact function of this brush isn’t known. It matches very well with 19th century brushes used in foundry work, but the same basic style of brush is used in a huge variety of applications from bricklaying to cleaning the house. You may have a very similar brush (although probably with a handle) with a dustpan at home!
This particular example is made of birch, with clusters of plant fiber bristles bound together. The binding material has not survived, so was likely thread or hair rather than a metal wire. The backs of these bound bristle clusters were inserted in holes in the brush, and a thin wooden veneer glued over the back of the brush to hide the holes. There would also likely have been an adhesive such as pitch or rosin holding the bristles in place, but this material is no longer present – one of the reasons it takes so much time and support to keep them all in place now!
Work is still ongoing on this object; it still needs some additional chemical cleaning to remove the dark-colored iron staining. Once that is done the material can be bulked and stabilized, the object can be dried, and the temporary supports can all be removed. The bristles will never be strong or supple enough to actually use this as a brush again, but it’s always exciting when an object that began in concretion starts to look like it should again!
All images by staff of The Mariners’ Museum and Park.
References
Selvin, A. (2002) A Dictionary of American Hand Tools: A Pictorial Synopsis. Schiffer Publishing Ltd, Atglen PA.
Jones, M. (1974) The Story of Brushmaking: A Norfolk Craft. Briton Chadwick Ltd, Norwich UK.